High-impact decisions demand unparalleled accuracy.
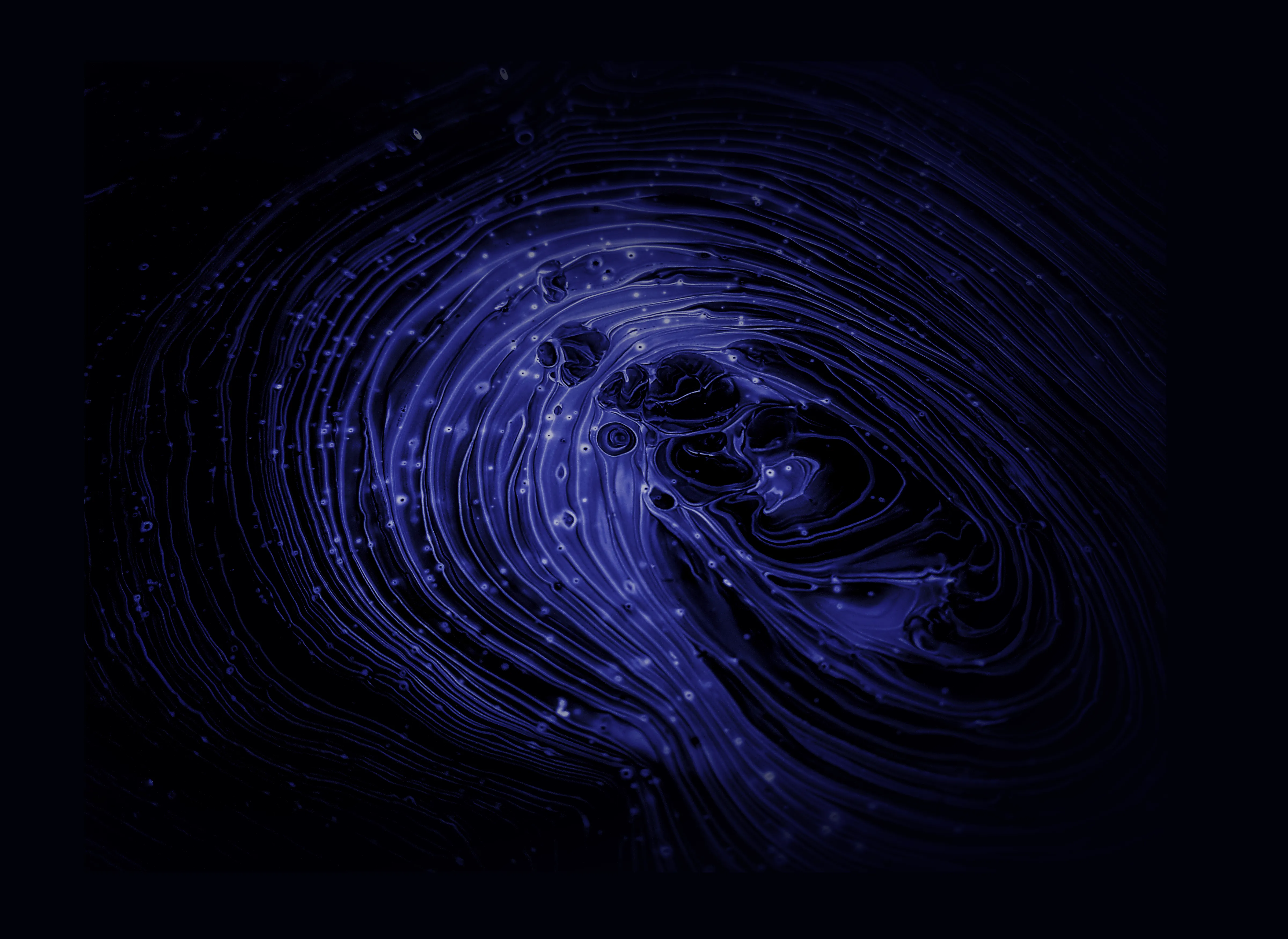
When it comes to the chemicals we use, we’re rarely given all the information. The impact of chemicals on environmental and human health isn’t well understood.
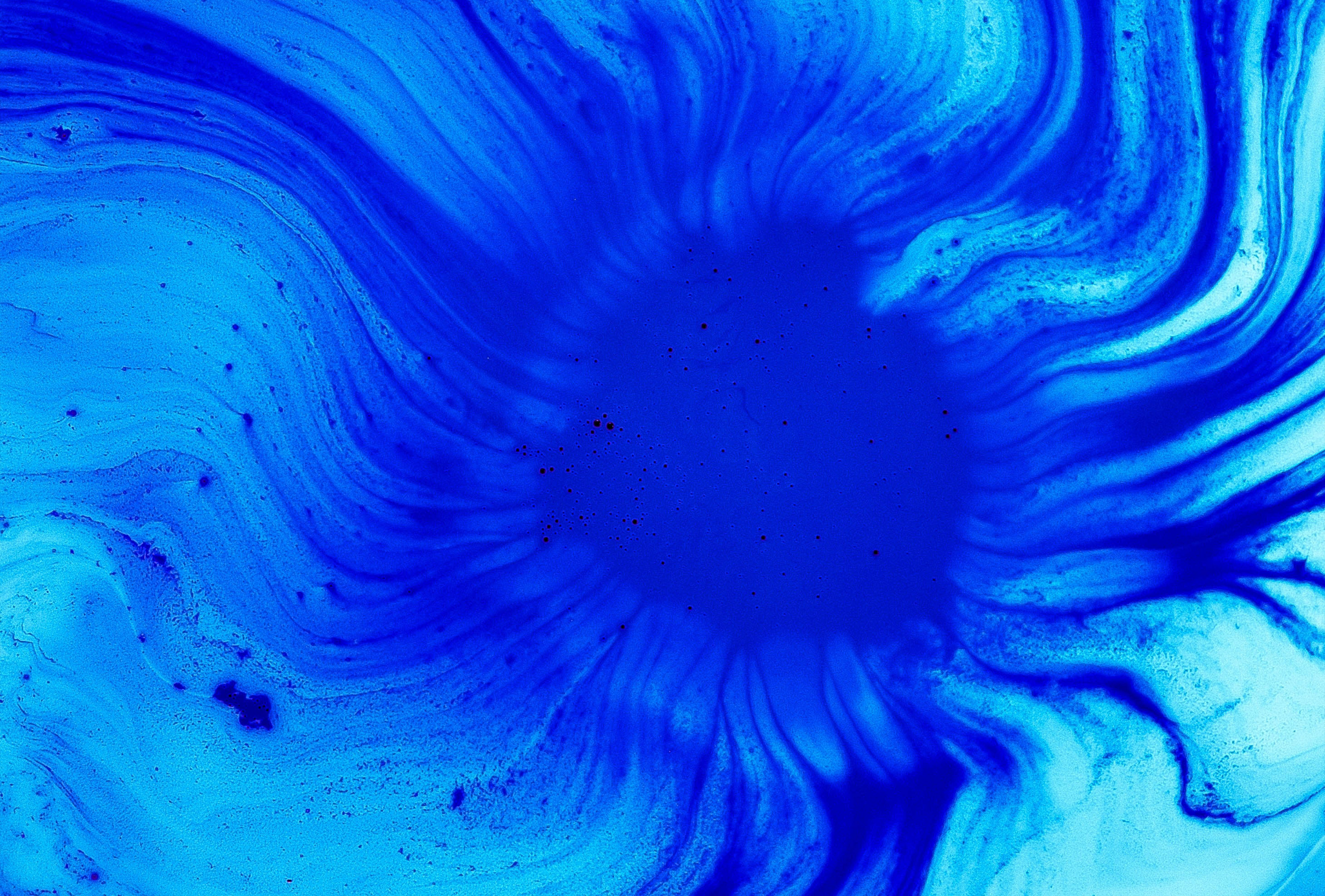
Get The Full Picture With ChemAlert

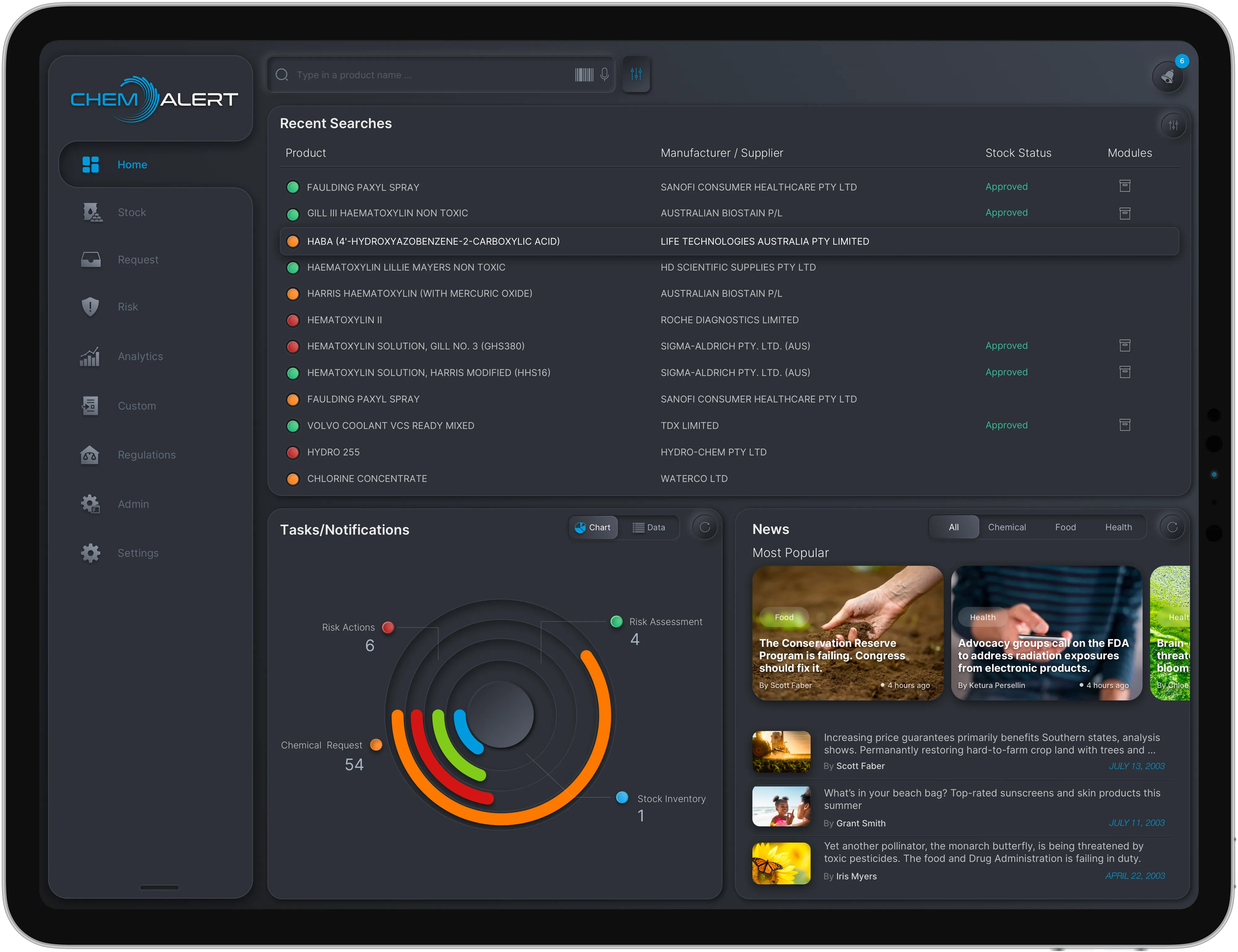
Give your team access to the information they need to make safer choices, everyday. With its easy to use interface, strict information quality standards and exceptional support, ChemAlert helps you protect what matters most.
DEMAND EXCELLENCE
Chemical Search
Quickly find the information you need by searching our database. With extensive filtering options, it’s easy to look for chemicals and chemical substitutes that fit your criteria.
Stock Inventory
Simplify the way you manage your chemical inventory. ChemAlert allows you to automatically create compliant stock registers, generate reports of hazardous or dangerous chemicals, track inventory and quickly identify storage incompatibilities and banned products.
Risk Assessments
We make risk assessments fast and simple, allowing you to customise your risk matrix to suit your business, pre-fill chemical hazard data and quickly identify tasks or chemicals with the highest exposure.
Hazard Labels
Easily find and print the latest GHS compliant labels in one click, or create your own customised labels.
Regions and Languages
Use the manufacturer SDSs for your region and work in your preferred language.
Intuitive Design
ChemAlert’s streamlined, user friendly interface makes it fast and easy for both seasoned and occasional users to navigate.
Safer choices start with accurate data.
Key Benefits
Manage Compliance and Reputational Risks
Transparent reporting on products within your supply chain that contain Chemicals of High Concern (CoHC).
Footprint Management
Measure your current chemical footprint, set targets for reduction and view suggested safer alternatives.
Research Reports
Access our scientists’ up-to-date independent reviews of every SDS inside our chemical library. ChemAlert Research Reports are available to download as a summary, extended summary and full report.
Product Alerts
Get notified of any discrepancies or issues between the manufacturer SDS and the ChemAlert Research Report, directly from our scientific team.
SDS Management
A ChemAlert subscription license gives you instant access to a centralized library of over 400,000 of the most up-to-date original manufacturer Safety Data Sheets (SDSs).
Colour Ratings System
A fast, visual indication of the hazard level a chemical represents for normal use. We use an easily understood colour system of green (low level hazard), amber (moderate level hazard) and red (high level hazard).
informed decisions
Simplify the way you work.
Request a demonstration to see first hand how ChemAlert can work for your company.
Our team will handle the migration of any pre-existing data and guide you to customise your solution to suit your preferences.
Attend complimentary introductory training and use the direct access to our Science and Technical Support teams to help you make the most of ChemAlert.
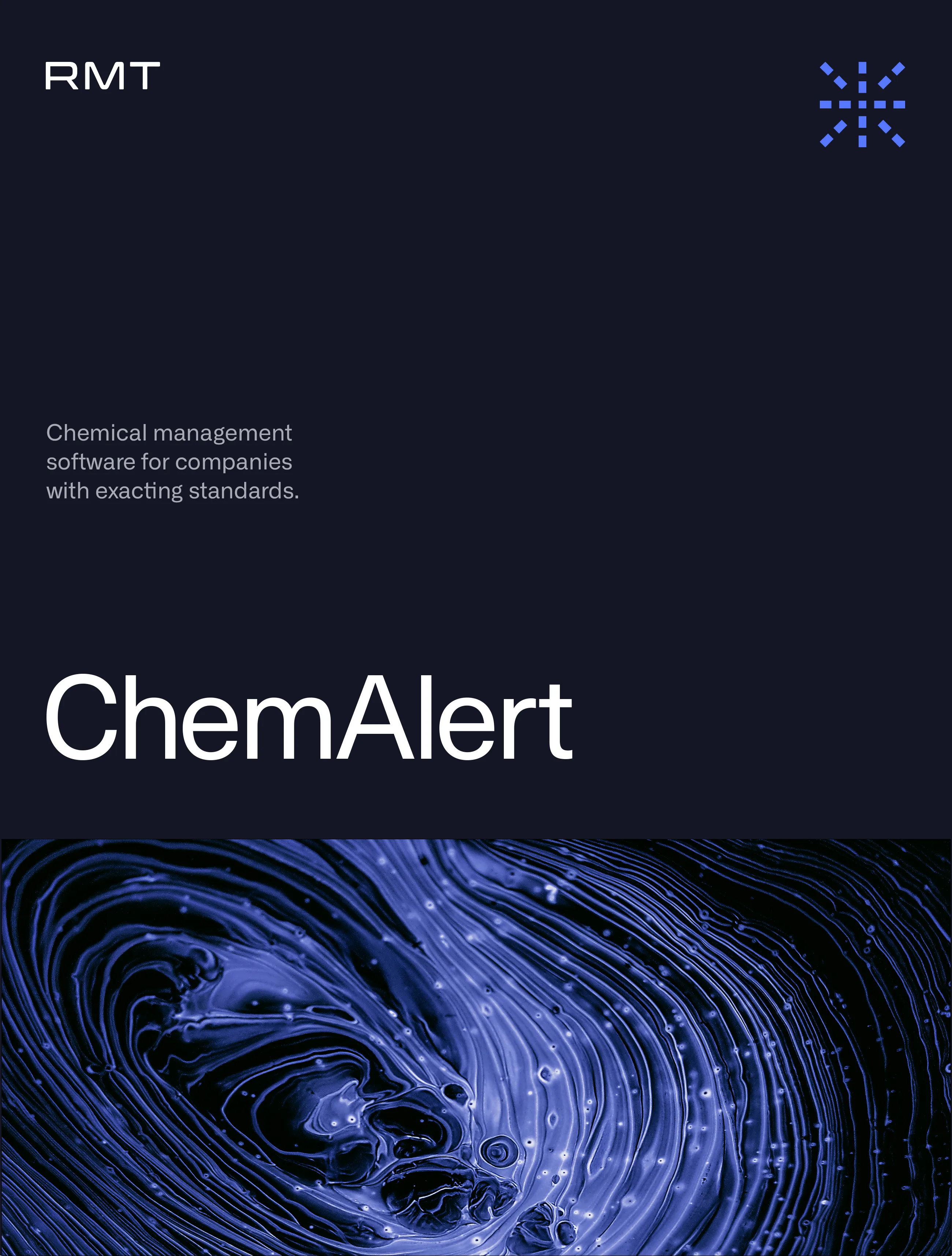
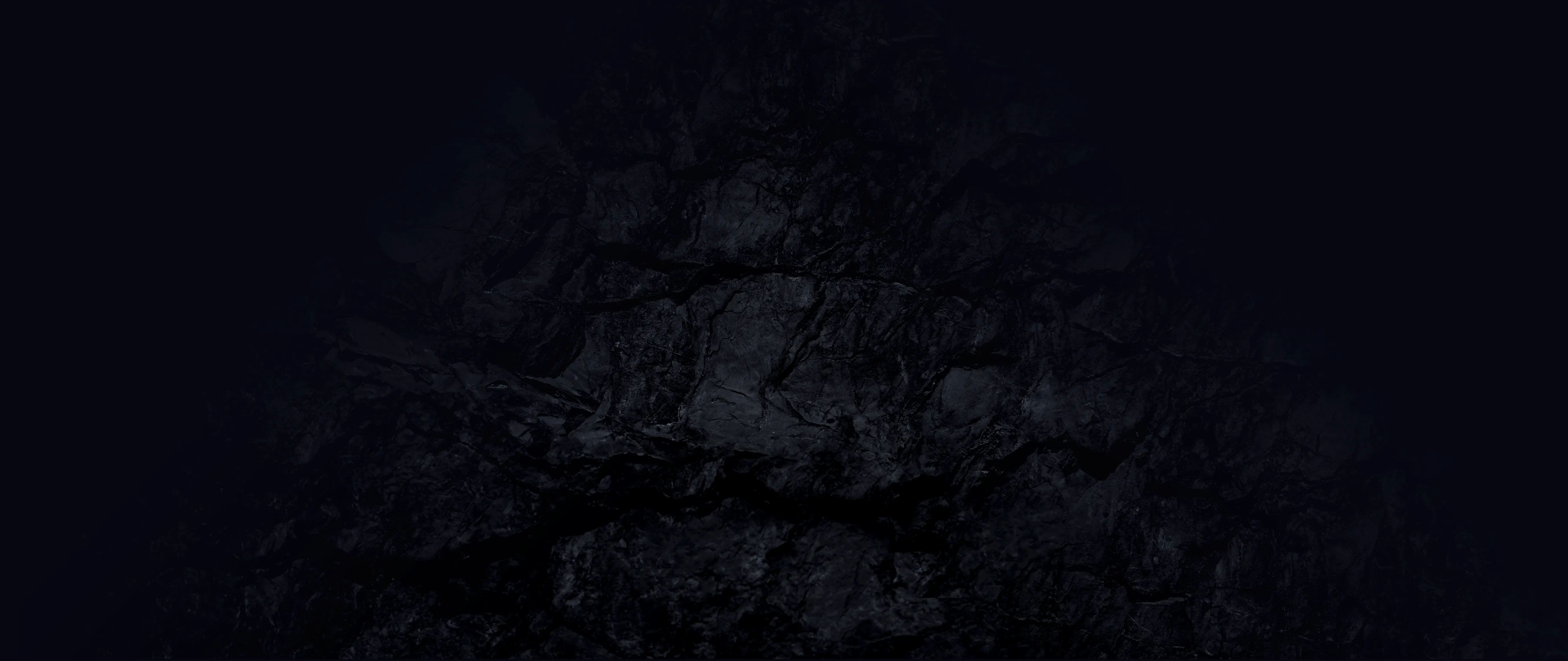